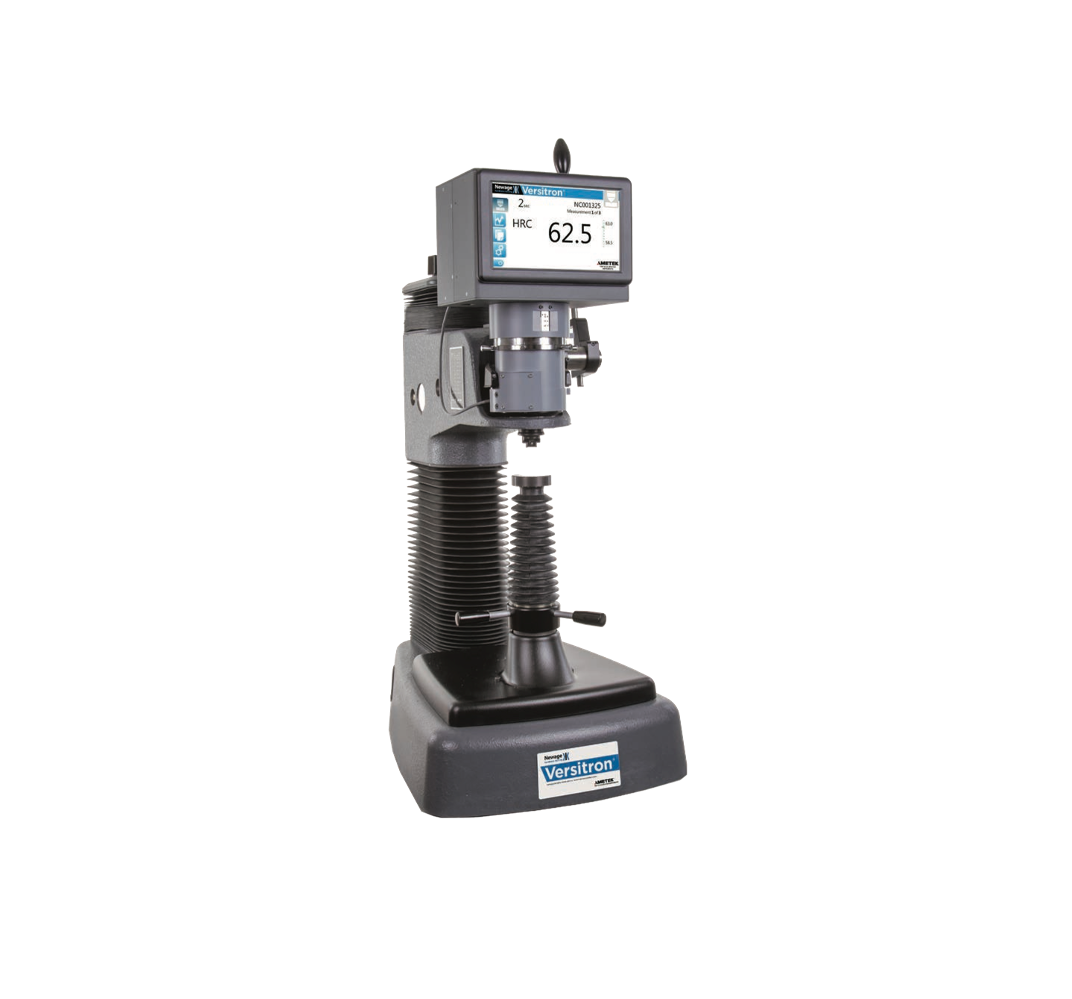
Newage Versitron Series Rockwell Tester
October 19, 2019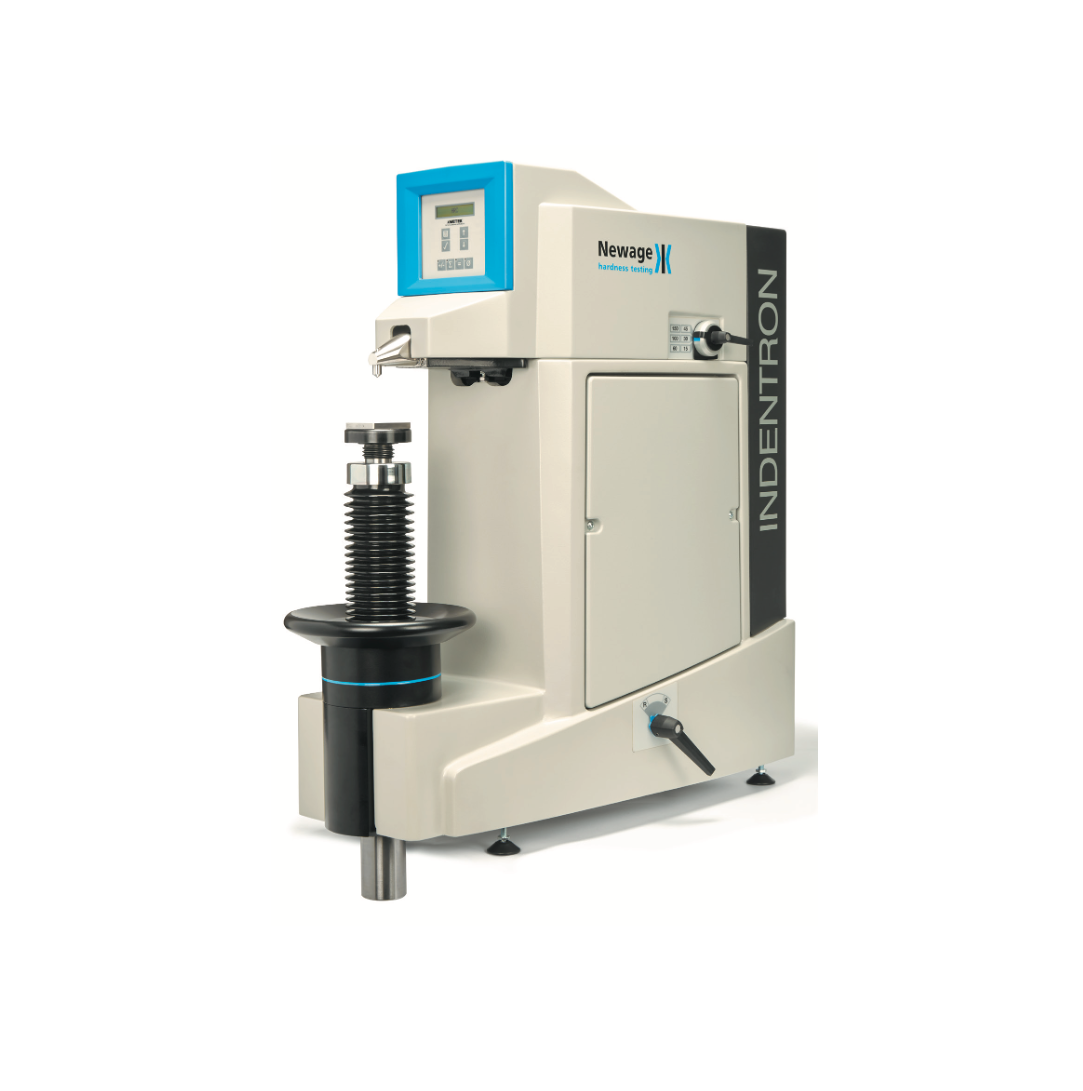
Newage Indentron Series Rockwell Tester
October 19, 2019Newage CPIT / CPST Tester
The Pin Brinell uses a unique method for the application of the test load. Force is applied to the indenter by means of either a hammer blow (Model CPIT Impact Load Tester) or through the C-clamp (Model CPST Static Load Tester). In either case, the force applied to the indenter is controlled by means of a calibrated expendable shear pin. This allows the system to be very portable and a perfect solution for large heavy course grain material components.
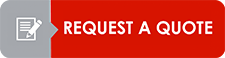
The Pin Brinell uses a unique method for the application of the test load. Force is applied to the indenter by means of either a hammer blow (Model CPIT Impact Load Tester) or through the C-clamp (Model CPST Static Load Tester). In either case, the force applied to the indenter is controlled by means of a calibrated expendable shear pin. This allows the system to be very portable and a perfect solution for large heavy course grain material components.
Details
Facts on the Pin Brinell
- The load to indentation size ratio provides a displacement that is equivalent to the most common Brinell test (3000 kg load, 10 mm ball) and the Brinell values are arrived at using the standard Brinell formula. The Pin Brinell tester makes an actual mechanical hardness test – it is not merely a test of other properties that correlate to Brinell values.
- A wide range of hardness can be checked from HB100 to 700. HB100 to 450 Brinell can be checked using the standard indenter and 300-700 Brinell using the carbide indenter.
- The shear value of each pin is measured during the manufacturing process. Based on this verification, pins are separated into lots having a variation less than 2%. These lots are assigned with letter designations (D, E, F, G, H). There is no difference in operation of pins between these different letter designations, so long as each pin is used with the appropriate chart that comes with the pins. Each type of pin covers the entire hardness range.
COMPARED TO THE IMPACT BAR METHOD
- Less Operator Influence on Test Results Only one optical measurement needs to be made. Consistent load regardless of operator technique. Can be as accurate as bench brinell testing.
- Easier to Use Each pin works in the entire hardness range HB100-700. Easier to test in confined areas. Only one impression needs to be measured. The Impact model is smaller and easier to use on large parts. The Static C-clamp model is easier to use on small or thin parts. Test impressions can be re-measured without retesting.
- Faster Operation One impression – one measurement. No additional computation required.
- Lower Cost Lower initial cost, lower operation cost.
COMPARED TO A HYDRAULIC C-CLAMP PORTABLE
- Impact model requires no clamping.
- Very low service requirements – fewer moving parts. So portable the Impact model fits in your pocket.
- Costs so much less to purchase.
- No messy oil.
- Much smaller and lighter weight.
- No need for recalibration.